ANSI 2 & 3 PPE, Equipment and Infrastructure Hi-Vis Striping
The Importance of Worker Visibility in Heavy Industrial Conditions
In heavy industrial environments, where machinery, vehicles, and workers work in close proximity, visibility is critical for safety. Ensuring workers are easily seen can prevent accidents, injuries, and fatalities. This is especially important in conditions where inclement weather, dust, dirt, and steam reduce visibility. Choosing the right high-visibility workwear can make all the difference.
Why ANSI 2 and ANSI 3 Outperform ANSI 1 in Heavy Industry
ANSI/ISEA 107 sets the standard for high-visibility workwear, categorizing garments into three classes based on the level of risk in different work environments. While ANSI Class 1 garments provide minimal visibility for low-risk settings, they fall short in heavy industrial conditions where hazards are abundant.
ANSI Class 2: Offers increased visibility with a minimum of 775 square inches of background fabric and 201 square inches of reflective material. It is ideal for work near moving machinery and moderate traffic areas.
ANSI Class 3: Provides the highest level of visibility with at least 1,240 square inches of background fabric and 310 square inches of reflective material, ensuring workers remain highly visible even in extreme conditions.
Challenges of Heavy Industrial Environments
- Inclement Weather: Rain, fog, and snow can significantly reduce visibility. ANSI Class 2 and 3 garments ensure workers are seen even in poor lighting and harsh weather conditions.
- Dust and Dirt: Many industrial job sites are filled with airborne particles that obscure vision. High-contrast and retroreflective materials in ANSI 2 and 3 garments cut through the visual noise, keeping workers distinguishable.
- Steam and Heat: Environments with steam, such as manufacturing plants and refineries, create optical obstructions. Superior visibility gear ensures workers remain identifiable.
- Fast-Moving Equipment: Heavy industrial settings often have forklifts, cranes, and other large machinery operating at high speeds. Workers in Class 2 or 3 gear are more likely to be noticed, reducing accident risks.
The Safety Benefits of Superior Visibility Gear
- Reduced Risk of Accidents: High-visibility workwear enhances worker detection, helping operators of heavy equipment spot personnel from a greater distance.
- Compliance with Safety Regulations: Many industries require ANSI-compliant workwear to meet OSHA and workplace safety guidelines.
- Increased Confidence and Productivity: Workers feel safer when properly equipped, leading to better focus and efficiency on the job.
Conclusion
For heavy industrial workers, ANSI Class 2 and Class 3 high-visibility apparel is not just a recommendation—it’s a necessity. When faced with challenging environmental factors like weather, dust, and machinery movement, wearing superior visibility gear can mean the difference between a close call and a life-threatening accident. Employers and workers alike should prioritize high-quality, ANSI-certified workwear to ensure maximum safety on the job.
ANSI vs. Non-ANSI Reflective Striping – What is the Difference?
High-visibility workwear plays a crucial role in workplace safety, especially in environments where workers work near moving vehicles, heavy machinery, or low-visibility conditions. However, not all reflective striping meets the necessary safety standards. Understanding the difference between ANSI-compliant and non-compliant reflective striping is essential for ensuring worker safety and regulatory compliance.
What is ANSI-Compliant Reflective Striping?
ANSI-compliant reflective striping meets the American National Standards Institute (ANSI)/International Safety Equipment Association (ISEA) 107 standard. This ensures that reflective materials provide consistent brightness and visibility in both daylight and low-light conditions.
Key Features of ANSI-Compliant Reflective Striping:
- Meets ANSI/ISEA 107 standards for width, brightness, and placement on garments
- Uses retroreflective materials that return light directly to its source (e.g., headlights, infrared sensors)
- Ensures high visibility in low-light and nighttime conditions
- Required for Class 2 & Class 3 safety vests and workwear
- Works effectively with SEEN Safety System sensors for detection
Why ANSI Compliance Matters
- Regulatory Compliance – Meets OSHA, DOT, and industry safety standards
- Worker Safety – Enhances visibility, reducing accident risks
- Consistent Performance – Maintains reflectivity after exposure to washing, weather, and workplace conditions
What is Non-ANSI Reflective Striping?
- Non-ANSI reflective striping does not meet established safety visibility standards, which can put workers at risk
Common Issues with Non-ANSI Reflective Striping:
- Too narrow or dim, providing insufficient visibility
- Lacks retroreflective properties, scattering light instead of directing it back
- Fades, cracks, or loses reflectivity quickly
- Not designed to meet OSHA, DOT, or industry requirements
- May not be detectable by SEEN Safety System sensors
How This Affects SEEN Safety System Users
The SEEN Safety System detects reflective materials using infrared technology. If workers wear non-ANSI compliant gear, the system may not recognize them properly, reducing safety effectiveness. To ensure full visibility, workers should always wear ANSI Class 2 or Class 3 certified reflective safety workwear.
How to Identify ANSI-Compliant Gear
- Look for the ANSI/ISEA 107 Certification Label
- Check Reflective Striping Width – Must be at least 2 inches wide
- Test Visibility in Low Light – Should glow brightly under direct light
- Ensure Proper Placement – Reflective striping should be positioned for maximum visibility (torso, arms, and legs)
Conclusion
Regardless of whether you use the SEEN Safety System, selecting ANSI-compliant reflective workwear is essential for ensuring workplace safety, reducing accident risks, and maintaining compliance with industry regulations. Investing in the right high-visibility gear helps protect workers, improve visibility, and enhance overall safety performance.
Companies using the SEEN safety system include:
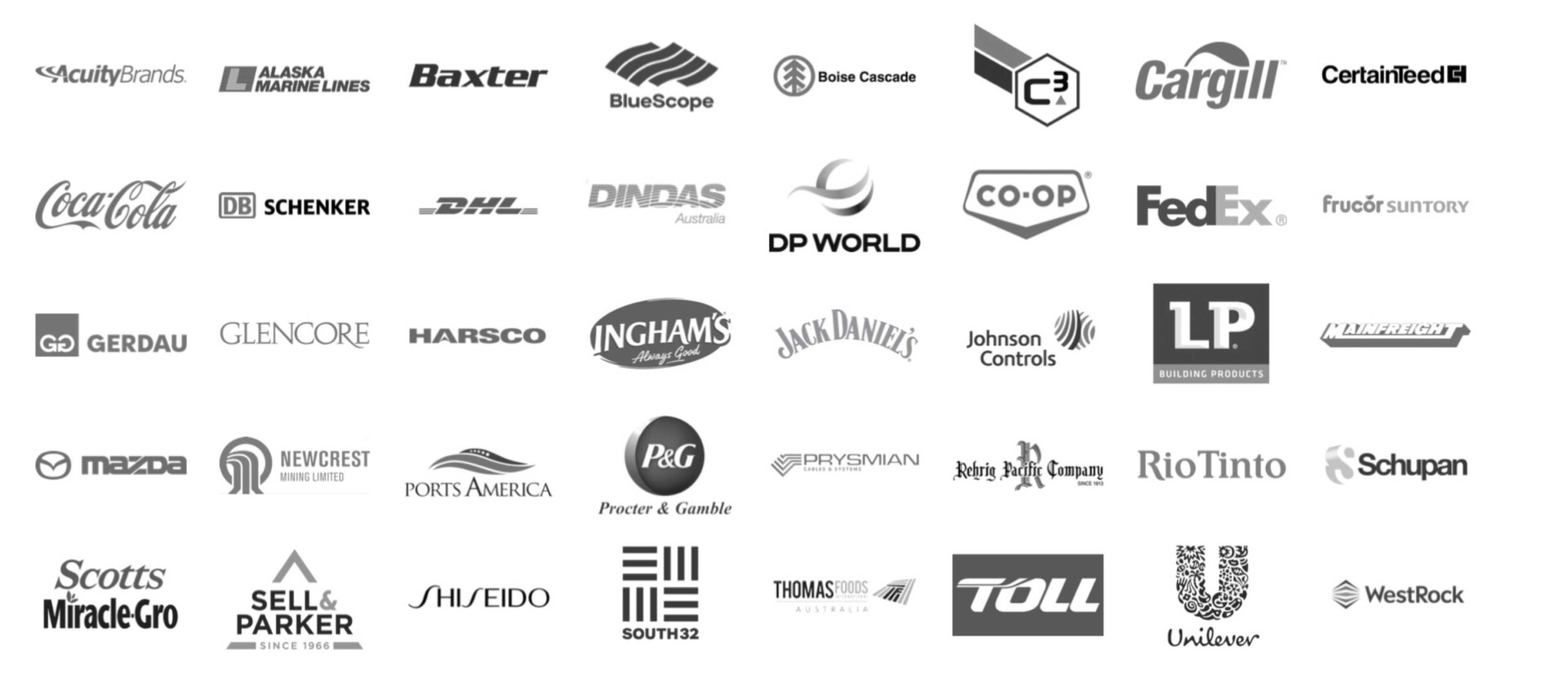
Let's Connect
To learn more or connect with us, please click below…