Selecting the Right Pedestrian Proximity Detection System
Step 1
Learn if SEEN is a good fit
Step 2
Use Checklist to help decide best fit
Step 3
Learn if you need a custom solution
Resources:
Selecting Safety Systems Checklist
Selecting Safety Systems
A checklist to use for picking the right “proactive” safety system for your business
When evaluating Safety Systems, consider the benefits of using an proactive system and its direct impact on the bottom line:
- Reduce OSHA incident rates, results in lower insurance premiums.
- Decreased legal fees.
- Less downtime, resulting in increased productivity.
- Minimized equipment damage costs.
- Preserved infrastructure integrity (such as buildings, doorways, production lines, and inventory storage racks).
SEEN Safety
SEEN Safety
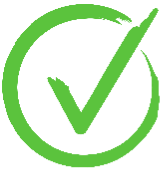
Active “real-time”
Detection
1. Passive or active?
Operational safety hinges on a blend of passive and active measures. While foundational safeguards like vests and procedures lay the groundwork, the critical second tier of active warning systems—like collision avoidance and proximity alarms—offers real-time detection and intervention. This dynamic approach not only combats human error and passive system limits, but also ensures immediate responses to risks, fortifying safety for workers, equipment, and critical infrastructure.
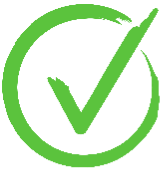
Active “real-time”
Detection
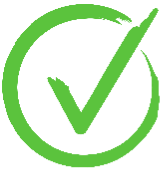
Selective detection
2. What to detect?
Certain radar systems detect anything within their range, alarming for various objects like walls, pallets, racking, and people. While helpful for preventing damage, they often produce too many alerts, reducing effectiveness. Selective detection systems, however, only alert for specific targets/tagged items, like people or load-bearing columns, disregarding irrelevant objects. This results in fewer, more actionable alerts, enhancing effectiveness.
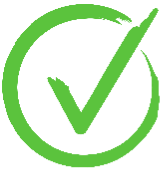
Selective detection
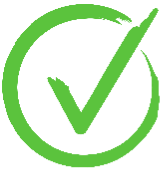
No tag needed or
complex AI processing
3. Tag or no tag?
RFID detection systems typically rely on electronic tags for reliable detection, but they come with challenges: – Tag issuance and training are cumbersome, especially with visitors and subcontractors. – Tags are costly, require regular charging and testing, adding expenses. – Integration with IT systems complicates deployment, and controlling detection zones can lead to over-reporting. – Alternatively, AI optical camera systems detecting humans, face reliability issues in adverse conditions such as dirty, wet environments, and demand intricate setup. Regardless of the system chosen, it should complement existing safety measures without necessitating behavior changes from workers.
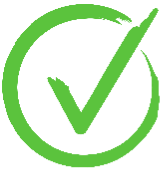
No tag needed or
complex AI processing
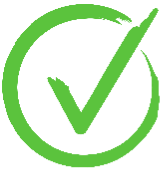
Precise detection zone
4. Detection area
Over-detection can nullify the effectiveness of any system. Finding the optimal balance within the detection area is essential for ensuring meaningful safety benefits without overwhelming operators with unnecessary alerts. When it comes to pedestrians in proximity to mobile equipment, a 360-degree detection approach could lead to an excess of alerts. Instead, focusing on targeted detection in critical risk zones proves more advantageous, providing support to operators without causing undue nuisance. Tailoring detection zones to individual machines and specific applications, can significantly reduce irrelevant alerts, thereby amplifying overall effectiveness.
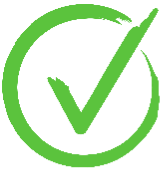
Precise detection zone
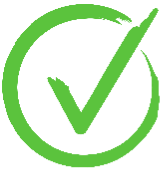
5. Operational impact
Downtime is costly. Faster, simpler installation gets machines back in operation swiftly, boosting earnings. Reliability is key; any technology failure results in expenses for repair or replacement. Plug-and-play systems with minimal setup lower overall ownership costs. Easy installation facilitates sensor transfer between machines as needed. Complex systems with multiple components, IT integration, and testing require staff training and oversight, adding to the total cost of ownership in terms of time and expenses.
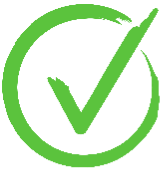
Simple to install and use
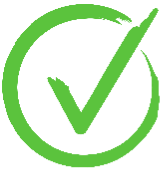
6. Tag fixed objects for detection
Along with prioritizing people, reducing the significant risk of collisions with other machines or objects is critical for many operations. Tagging allows for swift and cost-effective tagging of any object for detection. This creates greater integration operation to include mobile equipment and infrastructure.
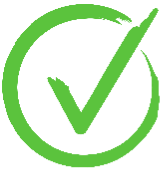
Tag any object with reflective tape
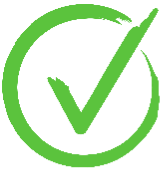
No ongoing cost
7. Cost
The costs for purchasing, installing, and maintaining a system dictate the number of sensors feasible for deployment. Even with an excellent system, if it’s too pricey to outfit all machines, the safety benefits won’t fully materialize, risking lives. Consider not only upfront expenses but also ongoing service and support costs.
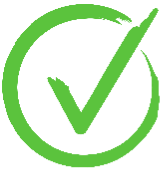
Affordable
No ongoing cost
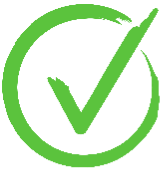
data reporting
8. Reporting / data / interoperability
Sensors are great at detection and warning, but when it comes to accident prediction and prevention, data is king. When evaluating a system, check that it has the capability to output data that can be used to provide meaningful and user-friendly insight into the near misses happening on your site.
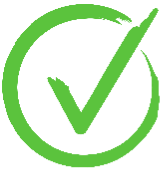
Critical incident data reporting
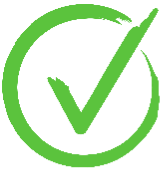
in all conditions
9. Reliability
Work sites pose challenges for high-tech sensors with factors like dust, dirt, weather, RF interference, and varying light conditions affecting their reliability. In physically demanding settings, simpler technology outperforms complex sensors. Evaluate the number of hardware components, maintenance needs, and the requirement for specialist support. Complex systems with regular support needs can escalate costs and frustrations rapidly.
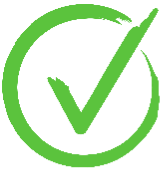
in all conditions
Companies using the SEEN safety system include:
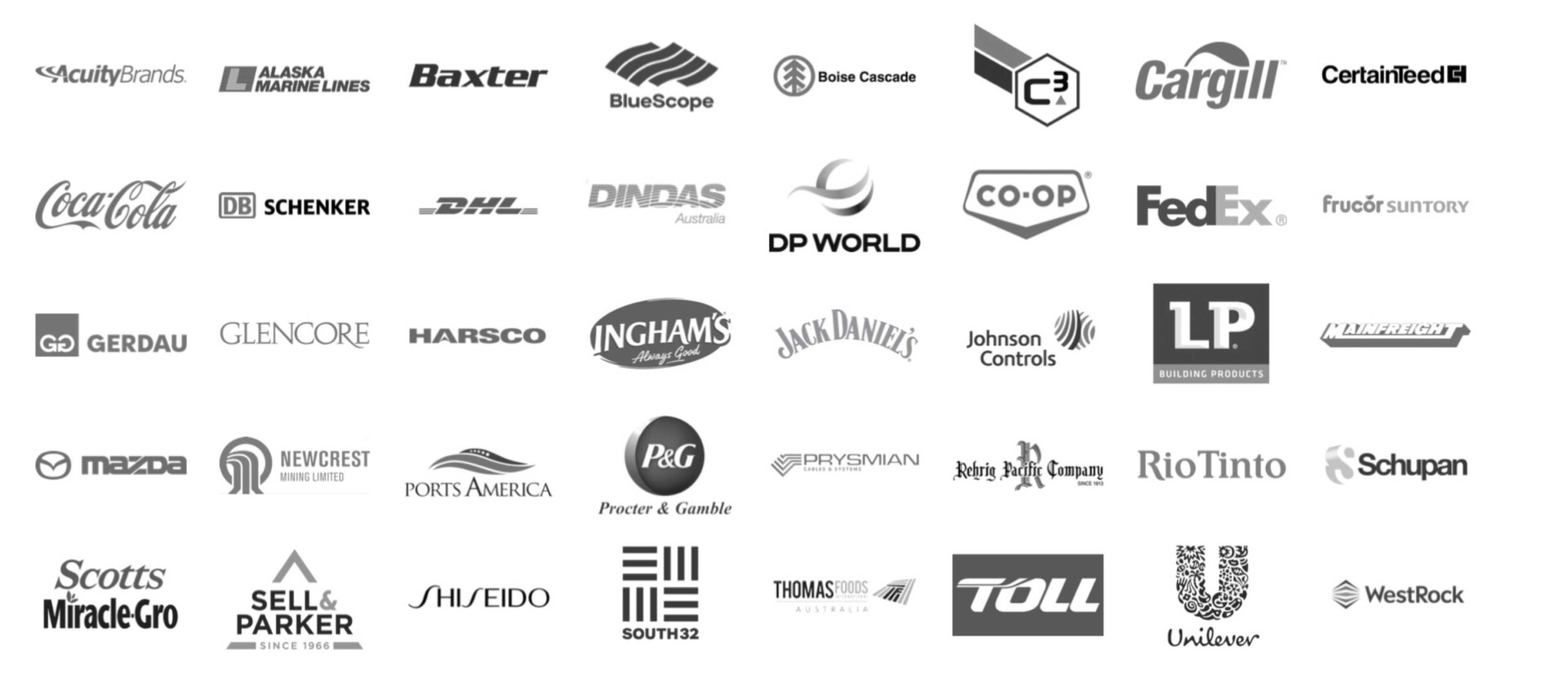
Let's Connect
To learn more or connect with us, please click below…